Case study
Power monitoring at
PIL Membranes
With energy costs rising, PIL Membranes were keen to start monitoring and optimising the power consumption of their machinery using low-cost technology.

PIL Membranes are key members of the Shoestring Community and helped Shoestring develop its first starter solution. Helping to take the beta version of the power monitoring solution to its first release, the Production Manager and Support Technician joined a cohort of companies to test, develop and deploy Shoestring’s basic power monitoring starter solution. Having seen first-hand the potential of the system, PIL has already started exploring more solutions, including one which will enable them to monitor more powerful machinery.
Harry Goldsmith, Support Technician at PIL Membranes, shared his learning journey with the power monitoring solution.
The business challenge
Harry joined PIL Membranes a year and a half ago straight from university and has played a key role in building and deploying Shoestring’s low-cost solutions on the shop floor. Harry explained the development process with Shoestring, highlighting how the power monitoring starter solution helped the company.
He said: “The amount of energy used across our site has become an increasingly important concern within PIL membranes in terms of the environmental impact and the cost of most of production being 24/7. The focus is to monitor the energy consumption of machinery to help optimise power usage. To carry out this monitoring we needed a cost-effective power monitoring solution which is easy to use, logs energy data on a frequent basis and can be accessed quickly.”
The solution
Harry said: “We went with the starter power monitoring solution using a Raspberry Pi 4 B (2GB) using the Gravity ADC module with a 20A CT clamp. The cost of these parts totalled up to just over £135 at the time we started the project.”
The costs of parts were:
- Raspberry Pi 4 Model B Starter Kit (2G): £79.50
- Italtronic Case for Embedded Raspberry Pi 4 Din Rail Enclosure, Grey: £15.61
- Gravity: I2C ADS1115 16-Bit ADC Module: £19.90
- AC Current sensor (SEN0211) with 20A CT Clamp: £20.95
The solution was installed on an exhaust fan on a production line. This was in an area with consistent enough Wi-Fi and with available electrical outlets to enable installation.
Harry continued: “The solution was built from scratch to a point where it was ready to be installed on a piece of machinery on two separate occasions. We started by working in a small test group to evaluate the first draft of the instructions. This was the first time we had worked using a Raspberry Pi, and we had little personal knowledge of our own internal network infrastructure. The setup of the beta version took place over four sessions of around three hours each across the span of three weeks. The time was spent understanding how a Raspberry Pi worked and working directly with Shoestring to help develop the instructions. The time was also spent understanding how we can allow the Raspberry Pi through our internal network to set a static IP to access the solution remotely.”
He added: “The solution was installed a few weeks later on an exhaust fan, but no data was being gathered. This was solved quickly once we got in contact with Shoestring where the problem was solved. Our internal network had its own NTP, and the RPi had not been directed to look at it; the solution worked well from that point onwards.
“The second time the solution was built was a few months after the initial install. This was with a revised version of the instructions and the knowledge we gained from the first install. The setup time for this was under 45 minutes.”
The outcomes
The data gathered from the exhaust fan showed that the power consumption was very stable with a variability of less than 0.1kWh. This data itself did not provide any improvement to the energy consumption, but it did work as great proof of concept for the Shoestring solution.
Harry said: “This solution has helped us gain a better understanding of how to use a Raspberry Pi to help ease the implementation of new solutions across site. The beta version of the power monitoring solution took a lot longer than expected but it paved the way for a greater understanding of how the solutions work and providing confidence to troubleshoot issues on our own before contacting Shoestring. This has also provided a greater understanding of the limitations of our network infrastructure of where we can and cannot gain network access as well as the measures needed to be taken to allow the solutions through the firewall.”
He added: “These solutions have opened communications between different departments – engineering and IT – to decide where and how the next solutions can be set up. This has shown that there is a high level of interest in this project, and it has given people the confidence to share ideas of where we can save energy in the future.”
What are the next steps?
Ryan said: “We are currently working on deploying an intermediate power monitoring solution which uses a multi-function meter to monitor machines which use much more power. The aim of this is to visualise voltage, amps, and power factor of a machine in real time and historically to be able to make informed decisions on which piece of equipment should have priority when it comes to maintenance. This solution is currently functional but is yet to be installed on a piece of equipment in the factory.
“Working in a cohort has been a fantastic way of learning about Shoestring solutions. We had regularly scheduled meetings with two other companies who were working on the starter power monitoring solution but using different hardware. This allowed us to discuss as a group how we were finding the solution and to share feedback amongst each other. We were able to bounce ideas off each other very easily and help one another if someone encountered any issues. The Shoestring team were very responsive to any contact we made and were able to issue concise support even when we didn’t fully understand the problem ourselves.”
Case study summary: PIL Membranes
Solution setup:
Business challenge:
Monitor the energy consumption of machinery to optimise power usage.
Solution:
Power monitoring solution, using open-source software and hardware which cost £135, which was initially installed on an exhaust fan on the production line.
Outcomes:
- Showed that power consumption on the fan was stable
- Provided a proof of concept for more digital solutions
- Provided greater understanding of the limitations of their network infrastructure
- Opened communications between different departments; gave staff confidence to share ideas of where we can save energy in the future
Next steps:
Installation of an intermediate power monitoring solution.
Find out more about this solution
Power
monitoring
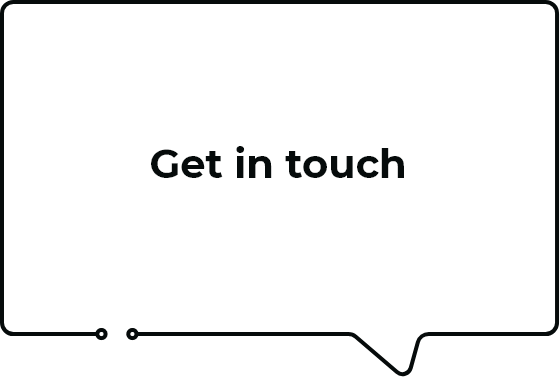