Job location tracking
Improve productivity with real-time visibility of jobs on the shop floor.
Shoestring’s job location tracking solution gives companies an easy way to get started and see how digitalisation benefits their business, building in-house digital skills along the way. The programme walks employees through the stages required to build and deploy the job location tracking starter solution, providing a practical learning experience.
Solve time-consuming problems
Quickly get answers to questions such as:
Where is a particular job right now?
How many jobs are waiting at a location or are in production, how long they been there?
Has a job been delayed or forgotten at a location?
The benefits
Shoestring’s job location tracking solution allows you to:
Quickly identify and address misplaced or delayed jobs
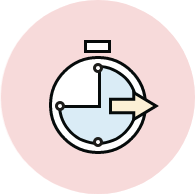
Spend less time finding jobs
Provide customers with instant updates on job progress
What’s needed from you?
A solution champion
Someone who will champion the solution deployment and make sure it gets the time and attention needed to make it a success (this person will get hands-on experience leading a digital project).
A solution implementer
Someone who will do what is needed to get the solution deployed (this person will develop practical digital skills – the only prerequisite is being interested).
How long does it take?
To deploy
The solution can be deployed in an afternoon once everything is ready. For most companies it takes 1-4 weeks to get everything ready (purchase the components, coordinate with their IT support, and set aside time for the implementer).
To use and review
4+ weeks: Once deployed, companies use the solution day-to-day for at least 4 weeks before we meet to review what has been learnt and what the next steps could be.
What you get:
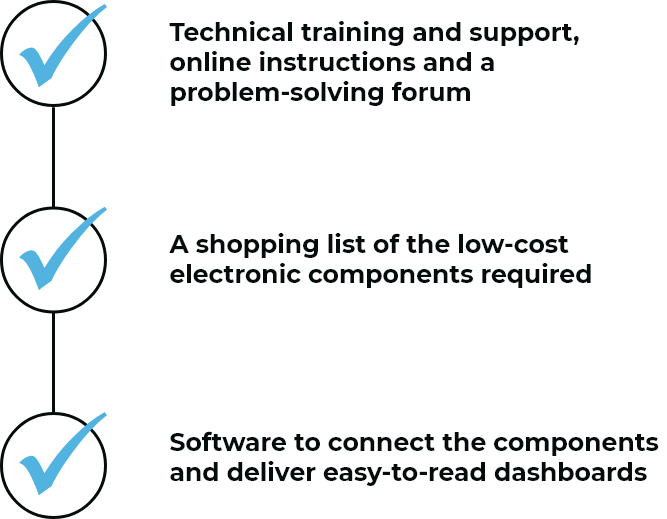
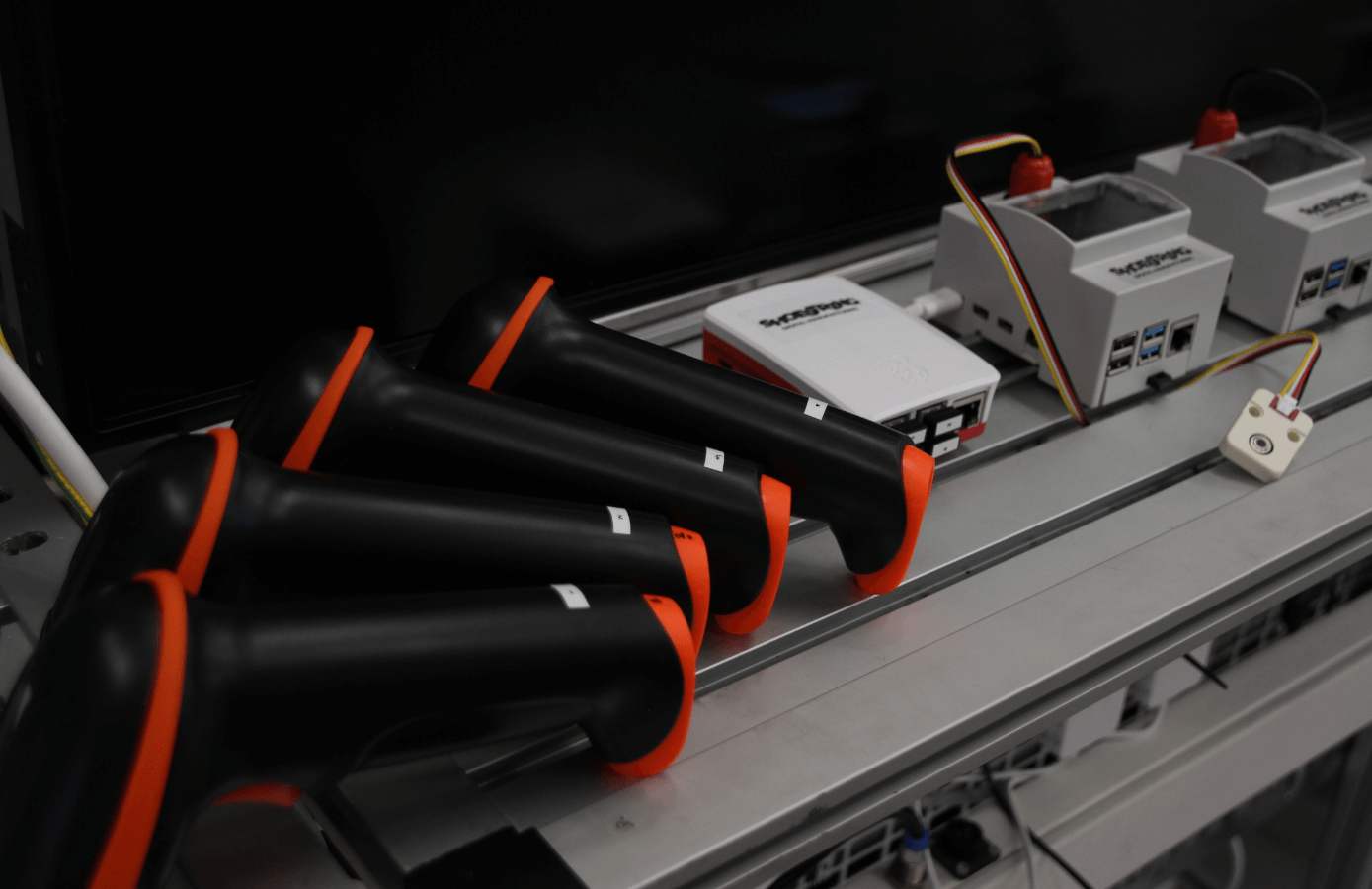
How the solution works
Using barcode scanners, your operations team can help capture data about the real-time location of jobs in production, which will then be presented on a dashboard, so that all jobs in the production line can be found instantly. This starter solution sets up two checkpoints on your shop floor to help your business trial job tracking.
How to set up the solution
Job location tracking is simple to set up and use. Here’s how:
- Set up two scanners located in two different locations
- Data from each scanner transmits to an easy-to-read live dashboard
- The dashboard shows where each job was last seen and how long it has been in this location
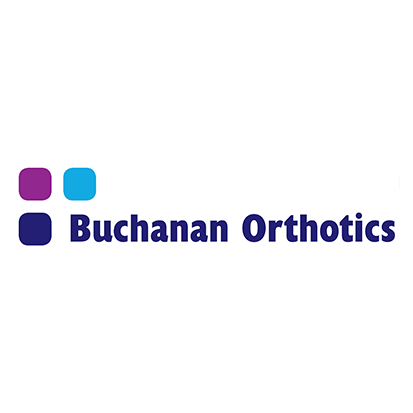
Case study:
Job tracking at Buchanan Orthotics
With a complex production process, involving a large number of both suppliers and customers, Buchanan Orthotics needed greater visibility of their production line but didn’t know where to start.
Choose another solution
Power
monitoring
Read more
Helps companies understand energy consumption by tracking actual equipment power usage.
Downtime
monitoring
Read more
Keeps track of machinery utilisation with real-time visibility of the reasons behind downtime.
Air quality
monitoring
Read more
Keeps track of the air quality of a factory or office space. This can be used to help maintain healthy and comfortable work conditions.